Former South Boston Rivet Factory Gets Heavy Timber Upgrade
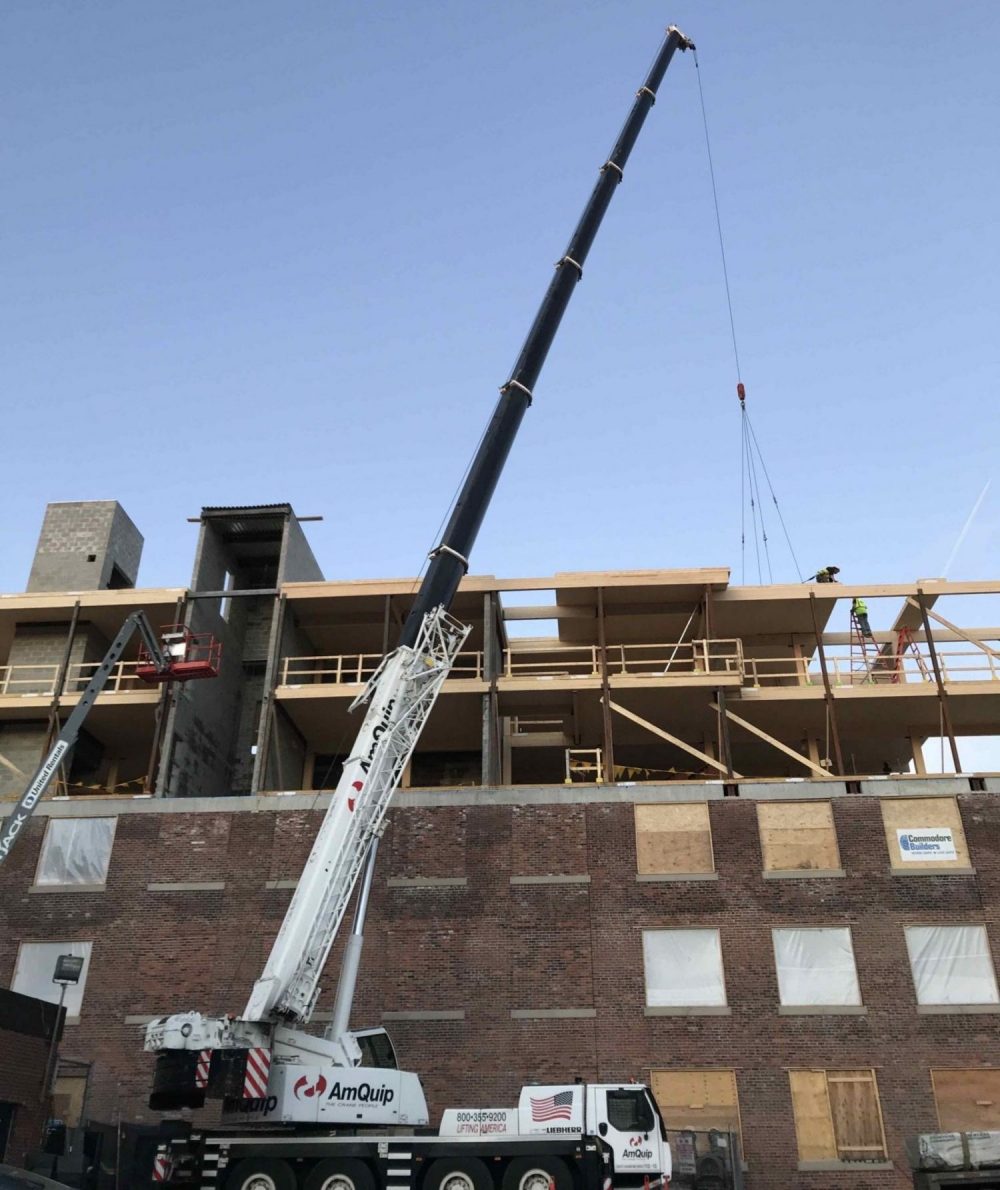
https://www.enr.com/articles/51022-former-south-boston-rivet-factory-gets-heavy-timber-upgrade
ENR New England
Author: Johanna Knapschaefer
Published: January 19, 2021
When first considering the addition of floors at a former South Boston rivet factory in 2018, the nonprofit owner CIEE Inc. quickly realized that installing a heavy concrete or steel system on top of the existing mass masonry heavy timber building would require significant work on the 120-year-old building’s foundation. Various bar joist and concrete solutions involved cost-prohibitive foundation upgrades to handle the added structural load.
Designers eventually suggested cross-laminated timber (CLT) for the future mixed-use building because it is roughly 25% lighter than concrete. “This was a no-brainer because it led to no foundation upgrades, except where we were adding an elevator core,” says Bryan Maltais, senior project manager for the project’s engineer of record, Boston-based McNamara Salvia Structural Engineers.
The $20-million 69-71 A Street project is Boston’s first renovation and expansion to incorporate CLT and the first of its kind in the U.S. An unrelated project underway in Boston’s Roxbury neighborhood, called Model C, is being erected with a CLT kit of parts to meet energy efficient passive house design standards. It will be one of the only buildings in Massachusetts built solely of ground-up CLT when finished this spring.
The A Street project team says adding CLT to an existing building as they did is more “challenging” than Model C’s ground-up CLT work. Maltais says hundreds of old buildings in the city built on urban fill with poor bearing capacity could benefit from A Street’s lightweight and cost-effective rehabilitation methods.
Nordic Structures, the project’s Montreal-based CLT fabricator and supplier, constructed a one-story CLT addition to an estimated 60-year-old, four-story building in Quebec. But the firm says nobody has attempted such a feat in the U.S. until now. Studying Nordic’s Quebec project and several other successfully completed CLT projects elsewhere helped CIEE overcome its initial reservations about becoming Boston’s earliest CLT adopter. Mariela Abreu, senior director and partner for the project’s owner’s representative, DBI Projects, says her client is pleased with the product’s performance and would consider it for future projects. “CLT stands out for its strength, appearance, versatility and sustainability,” she says.
The CLT Advantage
Construction on the South Boston project began in July 2019 and is on schedule for final completion by February. The five-story, 45,672-sq-ft mixed-use space employs 22,000 sq ft of CLT in the floors and ceilings of the two-story addition, according to the construction manager, Commodore Builders. It includes 1,650 cu ft of glued laminated-timber (glulam) beams and columns in three sizes and two lengths. There are 68 columns, generally 11.5 ft tall, and 137 beams between 12 ft and 14 ft long.
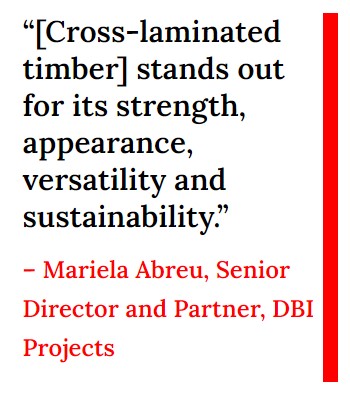
Unlike working with a typical metal deck and concrete—which requires close monitoring of winter weather conditions and site wrapping and heating before placing concrete—climate conditions hardly impact CLT erection, says Dan Hudd, senior project manager at Commodore. “Once the CLT comes out to the job, you pick it off the truck, set it in place and you can walk on it and work under it,” he says.
In addition to erecting each CLT floor in six days, “you could progress all the crews behind it,” Maltais says. The CLT floor is designed for 50 lb per sq ft of live loading, while the roof is designed for 100 lb per sq ft loading for a future roof terrace using a five-ply panel for both, with varying thicknesses on the inner plies. “The installed CLT doubled as the floor for each level and the ceiling for each level below it,” Hudd says.
Jean-Marc Dubois, Nordic director of business development, says the main challenge for the project’s CLT installation crew was the fact that the 80-ft tractor trailer delivering the wood had to navigate one-way streets and a narrow alley that was its final destination.
Cracking the Code
While the project team mostly relied on standard code, city officials “had never seen a project submitted with this material used in this manner,” says Nathan K. Turner, senior project manager and associate partner at Boston-based architect Margulies Perruzzi.
The team complied with existing Massachusetts building code—which uses the 2015 International Building Code as a base code—since the state code has no amendments for types of construction. “Since we were relying on CLT for our primary structural frame and floors,” Turner says, “we cross-checked subsequent sections in [the code] that noted heavy timber could be used for elements of a certain rating and confirmed compliance.” The team also aimed to be proactive in anticipation of Boston’s update to the international code in 2021, says Turner. The goal was to look at upcoming code changes and inform the city “we’re building against the 2015 code but keeping the 2021 code changes in mind,” he notes.
For example, the team chose a IIIA ordinary building type construction under the 2021 international code to renovate the older brick and beam building. It had new elements such as a one-hour fire rating rather than use of IV timber construction, which would have allowed construction up to 200 ft under new code changes but required a two-hour fire rating.
The builders opted to allow the primary black spruce members to remain exposed at the one-hour burn rate due to the large dimensions of wood columns and beams in the IIIA structure. The team calculated the char rate, understanding that the member will burn for a certain period before extinguishing but still be able to maintain up to 90% of its performance and to structurally keep all the load paths from what it is supporting, Turner explains.
The team found testing requirements for wood slabs and glulam were adequate for approval. “But when trying to use material with a slightly different application, the testing criteria wasn’t available yet, so the team had to borrow from U.S. and Canadian building code,” Turner says. But he predicts more testing resources should be available within six months.
Plumb of a Problem
The key to delivering the project came early in design. The design team spent a month in 2018 developing a proof of concept that proved to be the “most important driving factor” in solidifying CLT as the optimal material for the rehabilitation. But this proof of concept also revealed that the building’s existing conditions were challenging for incorporating CLT. “We were dealing with existing conditions with some geometries that weren’t true, meaning without 90-degree angles or parallel lines,” says Turner.
The builders maintained the existing structure while constructing the building core from the basement through three floors of the old structure. This required cutting out sections of existing flooring and shoring up everything before building the concrete masonry unit core, stairwells and elevator shaft. On the first three levels of the existing building, roughly 1,000 sq ft of the floor of each level was cut out to make way for the core. “We did our foundation work in the basement with our CMU core on top and brought that up, passing it through all the building floors, then tied all the floors back to that core as we went up,” Hudd says.
Transitions
Tying a “perfectly plumb structure” to an existing system with “irregularities” involved placing a concrete spandrel beam around the old factory perimeter, Hudd says. The team then added the CLT structure on top with a cornice sitting in front of the addition directly above the spandrel beam. But the cornice profile follows the existing building profile, sitting before the new structure so those transitions are concealed.
Stacking glulam columns on top of the existing heavy timber columns and beams made for an easy transition from the old structure to the new, Maltais says. “The CLT was installed in full-span planks on top of the beams and secured with self-tapping wood screws,” Maltais says. “Lag bolts were installed at the building perimeter to secure the CLT along the concrete spandrel beam.”
Additionally, the team connected double-height columns for the exterior structure to the CLT with wood lag screws. “In a steel frame structure, the columns would have been connected with larger anchor bolts, which would have been more time-consuming and costly,” Maltais says.
Since completing the core and shell in December, the team is currently in the project’s final inspection and acceptance phase. Says Hudd: “We are proud to have been able to use such an innovative and sustainable construction method on the project and hope that our use of CLT will pave the way for other developers who would like to consider alternative methods to traditional steel and concrete structures.”