Littleton Senior Center exceeds required stretch code during QA/QC blower door test
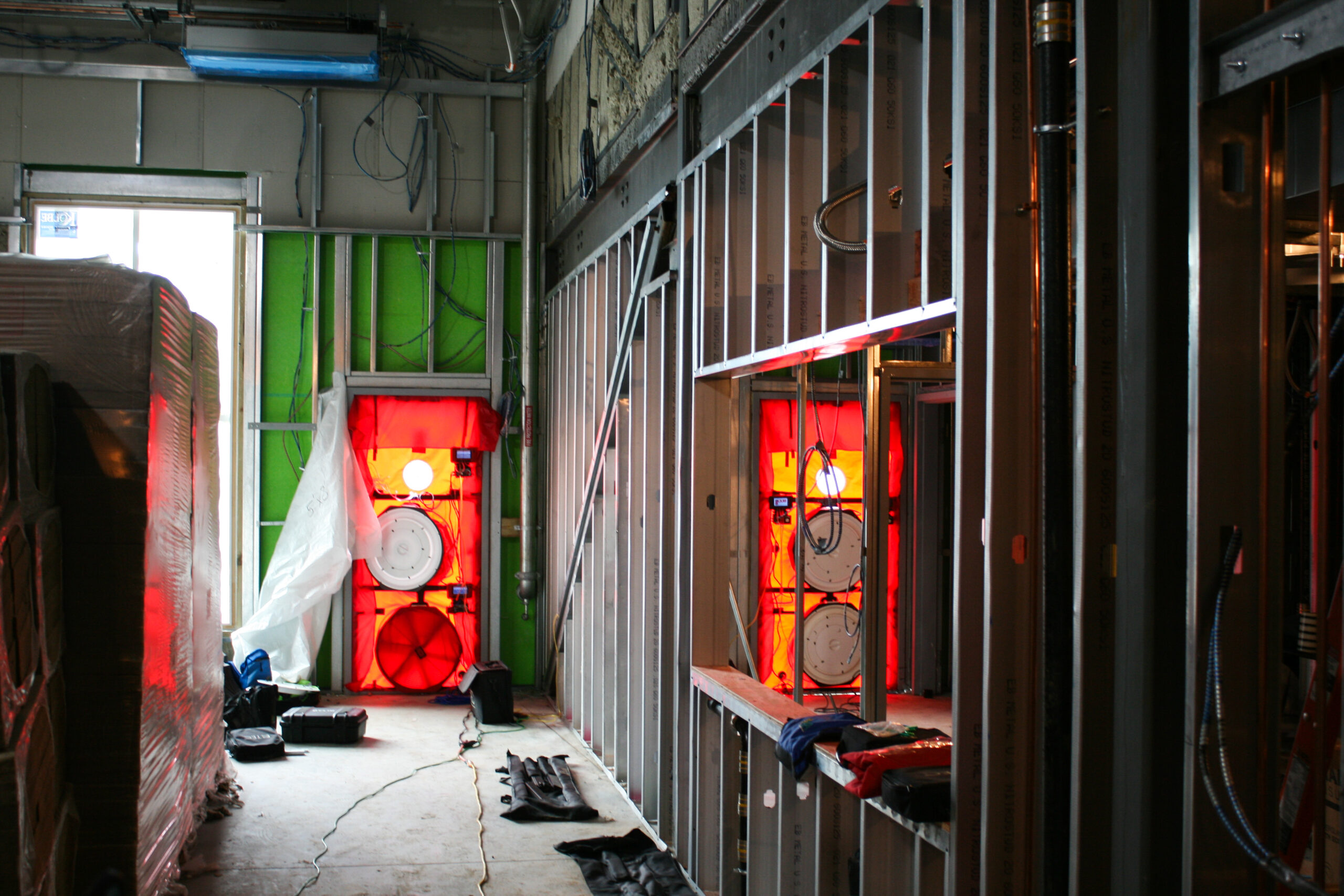
Exciting news! Our team at the Littleton Senior Center recently conducted a preliminary blower door test to evaluate the building’s airtightness as part of our Quality Control/Quality Assurance program. Thanks to the entire team’s diligence and quality control, we not only met but far exceeded the required stretch code air tightness requirements.
This achievement is a testament to the team’s meticulous planning, anticipation, and quality control.
Project Manager Sen Blankinship and Superintendent Al Tocci sought insights from fellow Commodore employees with Passive House experience to ensure this project could meet and exceed the Town’s stretch energy codes.
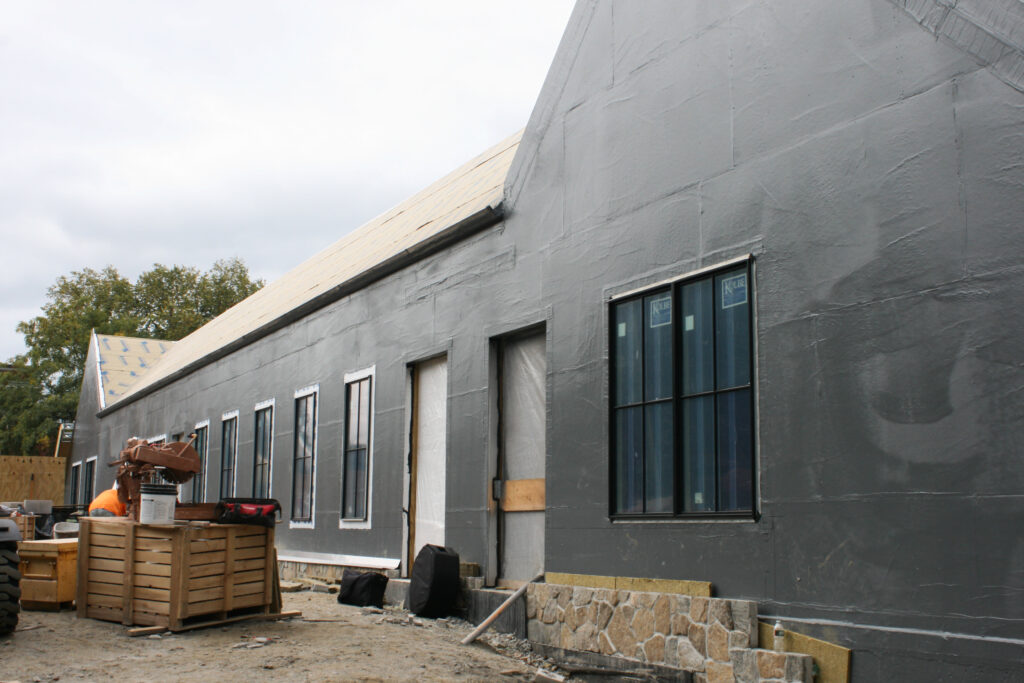
Often, blower door tests are completed after the building is completed, which can result in needing to navigate through interior walls to fix leaks and can add to the schedule and costs. Based on previous experience, we strategically scheduled the blower door test after fully applying the air and vapor barrier (AVB) but before closing the building. This timing ensured the building envelope was tight enough to yield accurate results, but with the walls still exposed, our team could quickly identify and rectify any leaks that could compromise the building’s energy performance.
Advanced Building Analysis (ABA), who conducted the blower door test, came well-prepared for even the most extreme leak scenarios. They arrived with four fans to ensure we could adequately pressurize the building, as well as thermal cameras and fog to help find leaks. However, thanks to the tightness of our building envelope, they only needed to use one fan to get results and even had to restrict the airflow further to pressurize the building.
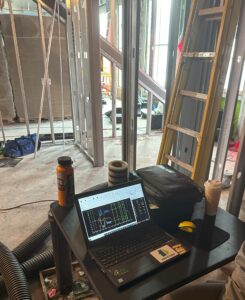
A crucial element of our success was the quality of work provided by our team. Notably, the waterproofing team was pivotal to our success. They first installed the AVB onto a building façade mockup that was then inspected by the AVB manufacturer. The team incorporated the AVB manufacturer’s recommendations and provided proper training for field personnel. An ABBA (Air Barrier Association of America) audit was also performed mid-way through the AVB installation, and their comments were fully addressed. These quality inspections significantly improved the integrity of the installed air barrier.
This achievement is just one example of how our team is proactively meeting the stretch code requirements for the Town of Littleton’s Senior Center. Conducting preliminary testing allows us to ensure quality early in the project, addressing any potential issues before they become costly or time-consuming. With these results in hand, we are well-positioned to move forward confidently as we prepare for the final, code-required test.
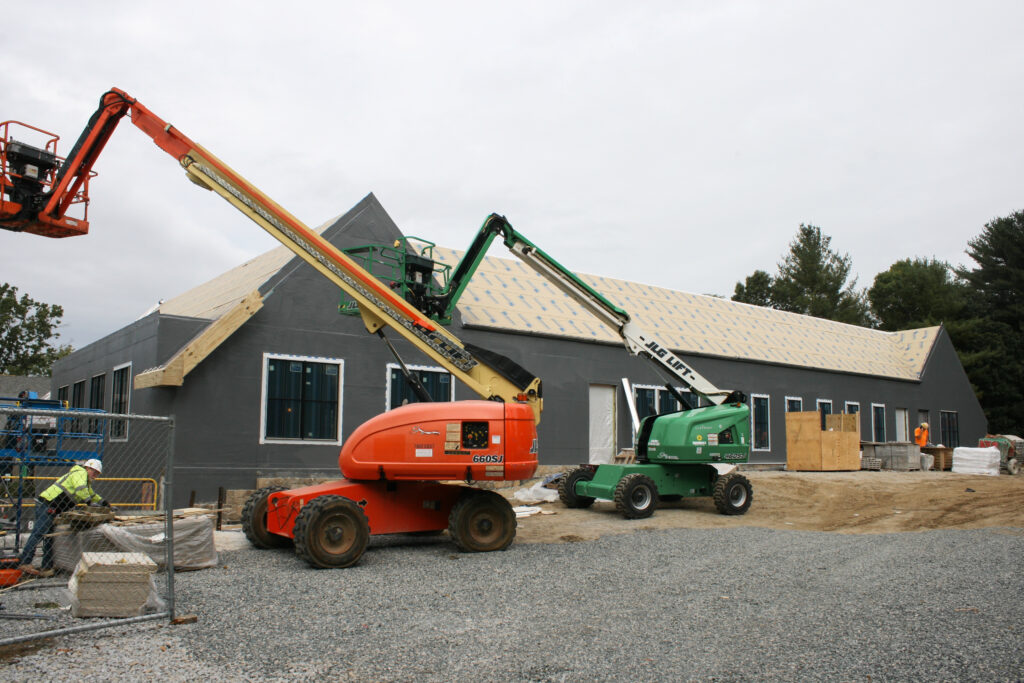